NBR 35L Rubber – NBR Rubber or Acrylonitrile Butadiene Rubber NBR 35 L
Introduction to NBR 35L Rubber
NBR 35L rubber is a type of nitrile rubber that is widely used in various industries due to its high resistance to oils, fuels and solvents. As a synthetic elastomer, this material is a combination of acrylonitrile and butadiene that offers unique mechanical and chemical properties.
What is Acrylonitrile Butadiene (NBR)?
Acrylonitrile Butadiene (NBR) is a type of synthetic rubber that is produced from the polymerization of two monomers, acrylonitrile (ACN) and butadiene. As a synthetic elastomer, this material is widely used in various industries due to its unique mechanical and chemical properties. Here is more information about this material:
Chemical Structure of Acrylonitrile Butadiene Rubber (NBR Rubber)
Acrylonitrile butadiene rubber is made up of two main monomers:
Acrylonitrile (ACN): This monomer is responsible for NBR’s chemical resistance to oils, fuels, and solvents. The higher the percentage of acrylonitrile in the compound, the higher the chemical resistance of NBR.
Butadiene: This monomer gives NBR its flexibility and abrasion resistance. Butadiene also helps improve mechanical properties such as elasticity and impact resistance.
The ratio of these two monomers in the NBR compound can vary and be adjusted based on specific industrial needs. In general, the percentage of acrylonitrile in NBR varies between 18% and 50%.
Properties of Acrylonitrile Butadiene Rubber (NBR Rubber)
Chemical Resistance: NBR has high resistance to oils, fuels, solvents and chemicals due to the presence of acrylonitrile.
Flexibility: The presence of butadiene makes NBR flexible and resistant to abrasion.
Heat Resistance: NBR performs well at moderate temperatures (usually between -40 and +120 degrees Celsius).
Abrasion Resistance: This material is ideal for applications that require abrasion resistance.
Lack of resistance to ozone and UV: NBR has little resistance to ozone and UV and may degrade over time.
Applications of Acrylonitrile Butadiene Rubber (NBR Rubber)
Acrylonitrile Butadiene Rubber is used in various industries due to its unique properties, including:
Automotive Industry: Manufacturing gaskets, O-rings, fuel and oil hoses, and engine parts.
Oil and gas industry: Production of oil and fuel resistant parts, such as valves and seals.
Food industry: Production of parts that come into contact with oils and fats.
Medical industry: Production of disposable gloves and chemical resistant parts.
General industry: Production of conveyor belts, rollers and wear resistant parts.
Advantages of acrylonitrile butadiene rubber (NBR rubber)
Excellent resistance to oils, fuels and solvents.
Flexibility and wear resistance.
Relatively low production cost compared to other elastomers.
Good performance at medium temperatures.
Disadvantages of acrylonitrile butadiene rubber (NBR rubber)
Low resistance to ozone and ultraviolet radiation.
Limitations in applications with very high temperatures (above 120 ° C).
Lack of resistance to some strong solvents such as acetone and chloroform.
NBR’s difference from other rubbers
Compared to natural rubber (NR): NBR has better resistance to oils and fuels, but shows less flexibility at low temperatures.
Compared to EPDM: EPDM has better resistance to ozone and atmospheric agents, but its resistance to oils and fuels is lower.
Compared to silicone: Silicone has better heat resistance, but its production cost is much higher.
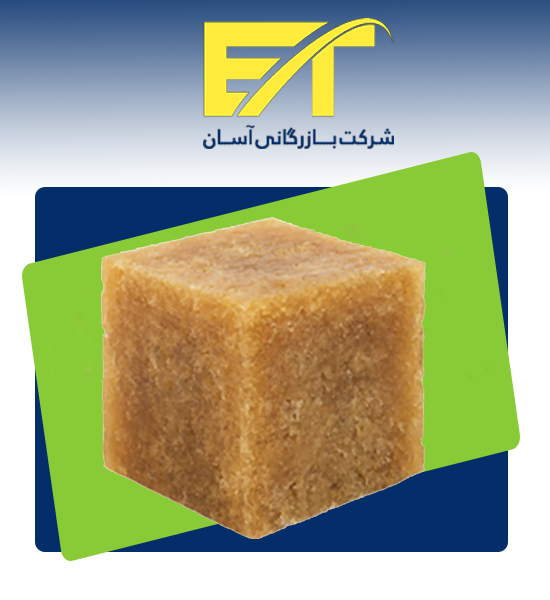
NBR 35L Rubber Production
The NBR 35L rubber production process involves the emulsion polymerization of acrylonitrile and butadiene. This process is carried out in the presence of catalysts and special chemicals to create the desired molecular structure. After polymerization, additives such as stabilizers, plasticizers and fillers are added to the mixture to improve the final properties of NBR 35L rubber.
NBR 35L Rubber Applications
NBR 35L rubber is used in various industries such as automotive, oil and gas, food and medical industries. This material is used in the manufacture of gaskets, O-rings, hoses and parts resistant to oil and fuel. It is also used in the production of industrial gloves and medical equipment.
NBR 35L Rubber Maintenance
To extend the life of NBR 35L rubber, it should be avoided from direct sunlight, high temperatures and strong chemicals. Keeping it in a cool, dry environment away from oxidizing agents helps maintain the properties of this material. It is also recommended to regularly clean parts made of NBR 35L rubber with mild detergents.
Advantages of NBR 35L rubber
NBR 35L rubber is one of the best choices for industrial applications due to its high resistance to oils, fuels and solvents. This material also has good flexibility and performs well at low temperatures. In addition, its relatively low production cost makes it economical compared to other elastomers.
Disadvantages of NBR 35L rubber
Despite its many advantages, NBR 35L rubber has low resistance to ozone and ultraviolet radiation and may crack or degrade over time. Also, this material may lose its properties at very high temperatures and is not suitable for very high temperature applications.
Factors Affecting the Price of NBR 35L Rubber
The price of NBR 35L rubber is affected by various factors such as the price of raw materials (acrylonitrile and butadiene), production costs, global market fluctuations and industrial demand. Also, the quality of additives and production processes can affect the final price of this product.
Environmental Impact on NBR 35L Rubber
Due to its synthetic nature, NBR 35L rubber is not biodegradable and may be harmful to the environment. However, recycling and reusing parts made from this material can help reduce its negative impacts.
Comparison of NBR 35L Rubber with Other Elastomers
Compared to natural rubbers and other synthetic elastomers such as EPDM or silicone, NBR 35L rubber has better resistance to oils and fuels. However, it may perform worse against atmospheric agents and very high temperatures.
Research and Innovations in NBR 35L Rubber
Recent research on NBR 35L rubber has focused on improving its resistance to ozone and UV radiation. Efforts are also underway to increase its thermal resistance and reduce its environmental impact.
Choosing NBR 35L Rubber for Industrial Projects
When choosing NBR 35L rubber for industrial projects, factors such as the temperature range of application, the type of chemicals in contact, and the environmental conditions should be considered. This material is ideal for applications with continuous contact with oil and fuel.
The Future of NBR 35L Rubber in Industry
With the advancement of manufacturing technologies and the increasing demand for materials that are resistant to harsh conditions, the future of NBR 35L rubber in industry looks very bright. Innovations in the field of improving the properties of this material can create new applications for it.
Summary of NBR 35L Rubber
As a widely used elastomer material, NBR 35L rubber plays an important role in various industries. Considering its advantages such as high resistance to oil and fuel, flexibility and cost-effectiveness, this material will continue to be one of the top choices for industrial applications. However, paying attention to its limitations and conducting further research to improve its properties can help expand the applications of this material.
بدون نظر